Knapp 18 Kilometer Tunnel. Stück für Stück. So wird seit vergangenem Sommer der Fehmarnbelt-Tunnel, der längste Absenktunnel der Welt, in der riesigen Fabrik bei Rødbyhavn auf Lolland gebaut. Das erste Segment, also der erste Tunnelteil, wurde im Juli 2023 betoniert. Mittlerweile hat die Produktion an Fahrt aufgenommen. Auf den fünf Linien in den drei Fabrikhallen werden insgesamt 79 Standardelemente und auf der sechsten Linie, direkt neben der Halle C, zehn Spezialelemente produziert.
Die Standardelemente werden in neun Segmenten hergestellt. Diese Einzelteile werden aus einem Guss hergestellt. Sobald ein Segment betoniert und genug ausgehärtet ist, wird es ca. 25 Meter nach vorne verschoben, um Platz für die Betonage des nächsten Segments zu schaffen. Ab dem fünften Segment schauen die Tunnelelemente aus der Halle heraus – bis schließlich ein 217 Meter langes Element vor der Fabrik liegt. Dieser Vorgang wird sich in den kommenden Jahren noch etliche Male wiederholen.
„Statt diese leeren Rohbauelemente im Tunnelgraben abzusenken, bauen wir einen möglichst großen Teil der Ausstattung, die später im fertigen Tunnel benötigt wird, bereits vor dem Absenken in die Elemente ein. Das spart später viel Zeit und reduziert die logistischen Herausforderungen für die Arbeiten im abgesenkten Tunnel“, erklärt Markus Just, Bauingenieur beim dänischen Bauherrn Femern A/S.
„In der sogenannten Outfitting Area werden beispielsweise Dichtungen, Brandschutzverkleidungen und eine Vielzahl an anderem Zubehör eingebaut. Es darf allerdings auch nicht zu viel Innenausstattung sein, denn sonst sind die fertigen Tunnelelemente zu schwer und schwimmen nicht auf“, erklärt Just. Wenn diese Arbeiten abgeschlossen sind, wird das Element an beiden Enden mit Stahlschotten luft- und wasserdicht verschlossen und auf Verschubbalken weiter nach vorne geschoben. Die Schotten werden, nachdem das Element am Meeresboden platziert und mit dem Nachbarelement verbunden wurde, wieder von innen herausgenommen und in der weiteren Produktion wiederverwendet.
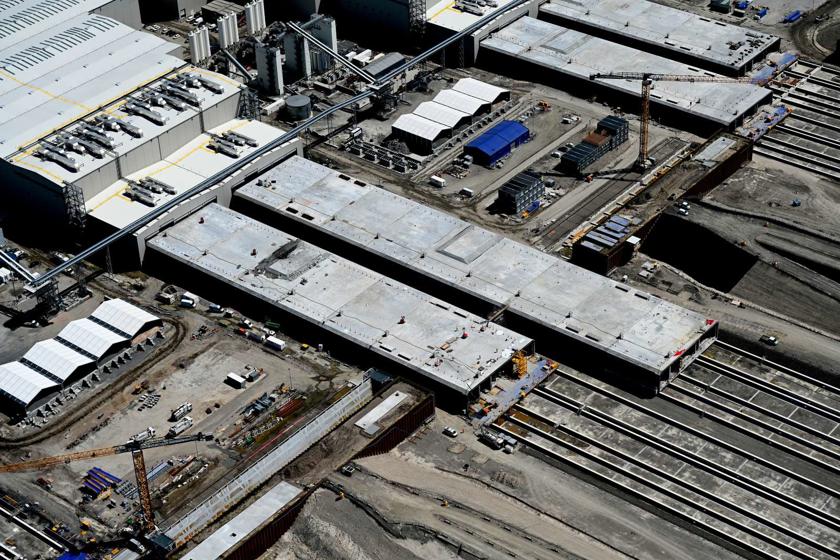
Doch noch ist das Tunnelelement nicht mit Wasser in Berührung gekommen. Das passiert im nächsten Schritt: Vor jeder der drei Fabrikhallen befindet sich ein Becken, das sich aus oberem und unterem Becken zusammensetzt. Die Becken sind von Deichen mit einer Deichkante von +10,80 Meter umschlossen und sind auf -10,80 Meter im unteren Becken ausgehoben. Wenn ein fertiges Element von einer der Fabrikhallen in den Arbeitshafen transportiert werden soll, wird das Ende des jeweiligen oberen Beckens mithilfe eines 110 Meter langen und elf Meter hohen Schiebetors verschlossen.
Der untere Teil des Beckens wird durch ein Schwimmtor abgeschlossen. Dieses Tor ist 45 Meter breit, 20 Meter lang, 21 Meter hoch und ist mit Pumpen ausgestattet. Das Prinzip ist ähnlich wie das einer Schleuse: Das Becken wird komplett geflutet, das Element schwimmt auf, wird mit großen Seilwinden zum tiefen unteren Ende des Beckens gezogen und der Wasserstand wird schließlich auf Meeresniveau gesenkt.
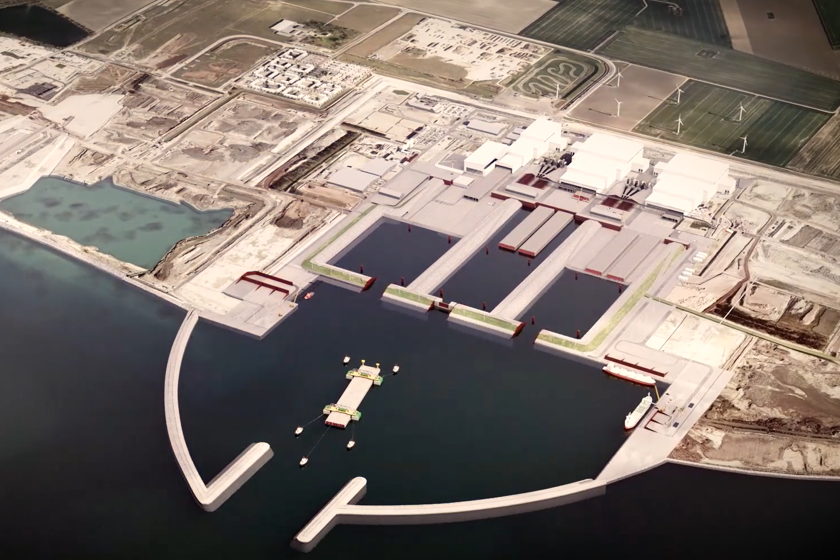
Nun wird das Schwimmtor geöffnet – bewegt wird dieses Tor mithilfe von Schleppern – und das Element wird in den Arbeitshafen transportiert. Dort wird es mit zwei Absenkpontons
verbunden, die es ähnlich wie Klammern halten. Zusätzlich wird noch Ballastbeton in das Element gefüllt, damit es später am Meeresboden nicht aufschwimmt.
Als nächstes tritt das Element seine Reise in den Fehmarnbelt an. Vier Schlepper transportieren es nun zur Absenkstelle. „Wenn sich das Element an der richtigen Stelle befindet, wird es an Stahlseilen abgesenkt und mittels Positionierung der Absenkpontons an das Tunnelportal beziehungsweise an die bereits abgesenkten Elemente herangeführt“, erklärt Bauingenieur Just.
Wenn sich das Element in der richtigen Position im Tunnelgraben befindet, werden die Dichtungen zusammengepresst und die Lücken zwischen den Elementen geschlossen. Das geschieht ganz ohne technische Hilfe, sondern rein mittels Wasserdrucks. Sobald das Wasser aus dem Hohlraum zwischen den Schotten von zwei Elementen gepumpt ist, stellt sich atmosphärischer Druck in der Kammer ein, und der Wasserdruck vom gegenüberliegenden Ende des Elements presst die beiden Elemente zusammen.
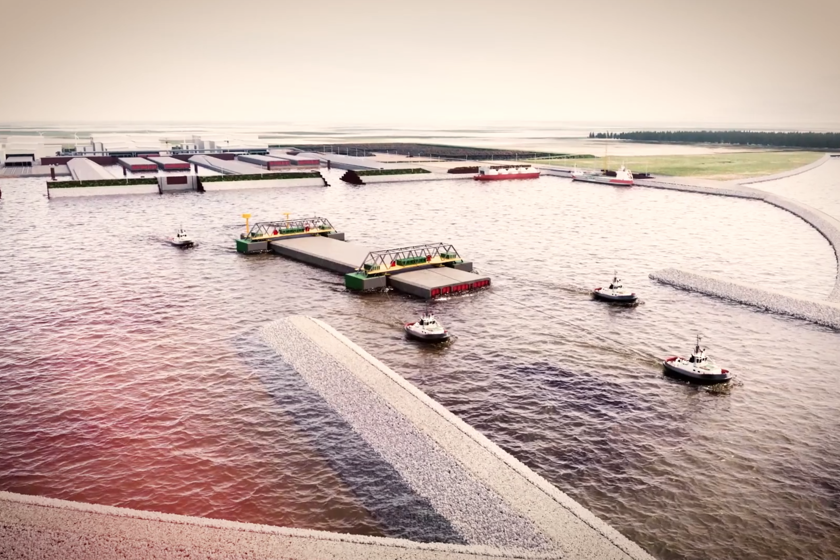
„Es erfordert eine sehr hohe Präzision, wenn die bis zu 217 Meter langen Tunnelelemente abgesenkt werden. Für diese Arbeiten wird ein eigens für dieses Projekt errichtetes Positioniersystem eingesetzt. Das System ermöglicht es, die Tunnelelemente für den längsten Absenktunnel der Welt mit einer Genauigkeit von wenigen Millimetern abzusenken und zusammenzufügen“, erklärt Markus Just.
Spezialschiffe werden auf den Tunnelelementen und seitlich davon eine Schutzschicht aus größeren Steinen aufbringen. Sie ist im Durchschnitt ca. 1,2 Meter dick und schützt das Element vor etwaigen sinkenden Schiffen oder Schiffsankern, die auf den Tunnel abgeworfen oder über den Meeresboden geschleppt werden. Die Meeresströmung wird dafür sorgen, dass der Tunnel im Laufe der Zeit wieder mit Sand bedeckt wird.